Introduction(介绍)
随着图形艺术行业越来越多地使用颜色显示器上的图像进行颜色评估和颜色验收(通常称为“软打样”),这种方法的需求逐渐增加。这要求颜色显示器及其相关的观看环境能够在标准图形艺术观察条件下模拟最终印刷图像的外观。为实现这一目标,通常需要组装一个软打样系统,该系统通常包括以下组件:
• 一台显示器;
• 一个用于校准和创建显示器配置文件并显示数据的软打样软件;
• 一台颜色测量设备;
• 一个标准光源观察箱
该系统的整体设计和校准必须控制并考虑环境光的影响。
随着软打样的使用逐渐增加,对软打样系统进行客观且与供应商无关的评估的需求也日益增长。本国际标准明确了从数字数据生成电子显示器图像的系统要求,这些图像旨在模拟由一组表征数据定义的印刷条件和由物理参考定义的专色。
本标准基于以下已有的相关标准:
• ISO 12646 中的显示器要求;
• ISO 3664 中规定的观察箱要求;
• ISO 12647-7 中规定的合同硬打样要求。
在软打样中,通常会遇到三种常见情景:
1. 显示器独立使用,无关联观察箱;
2. 显示器与观察箱结合使用;
3. 显示器嵌入并作为观察箱的一部分。
对于如何测试显示的图像与原始编码色度数据之间的相似性,无需区分这三种情景。然而,为了评估软打样再现与参考打印之间的相似性(如本标准所述),需要使用观察箱或受控的房间照明环境。
对软打样显示系统的客观评估分为三个步骤:
1. 测试显示器和观察箱,确保这些组件能够达到高质量软打样所需的结果;
2. 测试显示器与显示驱动软件的结合能力;
3. 评估输出条件(通常为表征印刷条件)的模拟效果。
在数据处理和显示驱动软件方面,将显示驱动与特定色度参考的模拟分开处理。显示驱动软件的主要目标是对显示器进行准确表征,这通常通过接触测量设备实现。
在评估显示设备本身后,还需评估显示设备与相关观察箱的结合(或用于模拟观察箱的房间照明设置)以及环境光的影响。对于从观察位置看到的显示器色度,模拟的表征印刷条件需进行测试,因此在此评估阶段需要使用遥测光谱辐射计。
当需要比较软打样与硬打样的印刷品时,通常会在显示器和观察箱的组合下进行,例如用于报纸或胶印印刷的评估。这种情况下,正在研究如何可靠地展示具体文档,以便在颜色差异争议中作为合同打样或参考。
在不受控环境光下使用独立显示器不属于本国际标准的范畴,因为软打样在显示器上的最终视觉外观无法忽略环境光的影响,即使在不与物理对象(如打样印刷品、生产印刷品或产品样本)比较的情况下也是如此。
实现参考标准的高质量软打样模拟并非易事,要完全准确地进行模拟需要对过程的多个方面进行精细控制。本国际标准的主要目的是建立评估完整软打样系统所需的标准和容差。
1 范围
本国际标准规定了从数字数据生成电子显示器图像的系统要求,这些图像旨在模拟由一组表征数据定义的特定印刷条件,以及由物理参考定义的专色。本标准就设备选择、设置、操作和环境条件提供了相关建议,并规定了与这些要求相关的适当测试方法。
2 引用标准
以下文档中的内容被规范性引用,并且对于本文件的应用是必不可少的。对于注明日期的引用文献,仅适用引用的版本;对于未注明日期的引用文献,适用其最新版本(包括任何修订)。
• ISO 3664:图形技术和摄影 — 观察条件
• ISO 12639:图形技术 — 印前数字数据交换 — 图像技术的标记图像文件格式(TIFF/IT)
• ISO 12646:图形技术 — 用于颜色打样的显示器 — 特性和观察条件
• ISO 12647-7:图形技术 — 半色调分色、打样和印刷品生产过程控制 — 第7部分:直接从数字数据进行打样的工艺
• ISO 15930:图形技术 — 使用PDF进行印前数字数据交换
ISO 14861:2015(第3至5页内容翻译)
3. 术语和定义
为了本标准的目的,适用以下术语和定义:
3.1 显示器(display)
一种能够以可见方式传递信息的电子设备。
3.2 特性化的印刷条件(characterized printing condition)
定义了过程控制目标的印刷条件,同时明确了输入数据(通常为CMYK色调值)与印刷图像的色度之间的关系。
来源:ISO 15930-8:2010, 3.1
3.3 关机(power off)
显示器(3.1)处于关闭状态的条件。
3.4 软打样(soft proof)
通过显示器(3.1)可视化色彩图像数据,旨在合成在定义的照明和观看条件下的颜色外观。
3.5 软打样系统(soft proofing system)
由硬件和软件组件组成的系统,用于在特定观察条件下再现颜色外观。
3.6 光谱辐射计(spectroradiometer)
用于测量在给定光谱范围内的窄波长间隔辐射量的仪器。
来源:IEC 60050-845:1987, 17.4
3.7 遥测光谱辐射计(telespectroradiometer)
使用光学中继组件以允许从样本一定距离进行测量的光谱辐射计(3.6)。
来源:ISO 13655:2009, 3.12
3.8 环境(surround)
图像边界附近的区域,其在观察图像时可能会影响眼睛的局部适应状态。
3.9 观察箱(viewing cabinet)
具有受控照明的区域(通常在侧面和背面封闭),提供特定强度和光谱功率分布,以实现样本的一致观察。
4. 要求
4.1 数据传递
软打样系统应接受以PDF/X文件格式(符合ISO 15930)或TIFF/IT文件格式(符合ISO 12639)传递的数字数据。对于TIFF/IT文件,颜色信息应包括在ISO 12639定义的标记34675或34029中。
注: PDF/X-1a要求注明预期的印刷条件。如果预期的印刷条件已包含在国际色彩联盟(ICC)维护的表征注册表中,并且数字数据为青色-洋红-黄色-黑色(CMYK),则通常使用ICC注册表中的名称进行标识,而不是包括ICC输出配置文件。如果未包含在注册表中,PDF/X-1a要求提供ICC输出配置文件。
4.2 显示器要求
用于软打样的显示器应符合ISO 12646中规定的A类或B类要求。
4.3 观察条件要求
4.3.1 General(总则)
视觉环境应被设计为最大限度地减少对观察任务的干扰。消除可能影响显示器图像评价和观察箱内打印品评价的干扰条件至关重要。软打样设置可能会有许多潜在的变化。为减少这些变化的影响,需要明确具体要求。
在本国际标准中,最终的颜色刺激将通过符合特定要求的仪器测量进行判断。因此,没有为显示器的位置提供额外的强制性要求。
主要存在两种设置环境:
1. 显示器位于观察箱旁边(但不在其内部):
在这种情况下,应控制环境以确保杂散光不会对显示图像或其周围区域产生显著影响。可以使用遥测光谱辐射计调整观察箱内的照度水平,使纸张的反射亮度(可能包含所模拟纸张的样张)与显示器中模拟的纸张亮度相匹配。如果所需的照度水平不同于 ISO 3664 中定义的 P1 或 P2 照度级别,应在 ISO 3664 的评估测试中额外测试此调整后的照度水平。
2. 显示器集成到观察箱内:
在这种情况下,例如当显示器放置在印刷机旁的观察箱内时,观察箱的照明可能会不可避免地照射到显示屏幕上。这时应尽可能减少观察箱的光线对显示屏幕的影响,例如使用遮光罩。对于此类系统,如果为了实现打印品和显示器之间的亮度和均匀性匹配而进行了补偿,观察箱的照明可能不在 ISO 3664 规定的限值范围内。
对于未在暗室中测试的没有专用观察箱的设置环境,应适用 ISO 3664 中定义的所有标准,确保待软打样的对象满足相关要求。
翻译基于标准术语,突出专业性和可操作性。如果需要更深入的解释或优化,请告知!
4.3.2 Displays to be used alone(独立使用的显示器)
对于独立使用的显示器(即不与观察箱结合使用),应遵循以下指导原则:
a. 显示器反射亮度控制:
在显示器关闭(关机)状态下,在显示器的表面(包括任何防反射屏后)放置一个完全反射的漫反射体,其亮度不得超过显示器白点亮度的四分之一(R=G=B=255,对于8位显示器)。
• 注: 这种控制方式可以将显示器反射引起的颜色变化限制在大约ΔE00=1(基于典型的现代平板显示器)。
b. 中性色环境:
显示器的边框、显示器周围环境(例如桌面、墙壁)及观察者视野范围内的所有物体应尽可能接近中性,避免饱和颜色元素对观察者的色彩适应造成影响。具体要求如下:
• 显示器边框: 灰色是最佳选择,但黑色或白色也可以接受。银色或铝制边框不适合,因为它们可能产生眩光。
• 墙壁和桌面: 中性灰色是最佳选择,但白色也可以使用。
c. 遮光罩的使用:
应使用显示器遮光罩来最大程度减少周围照明对显示器表面的反射影响。遮光罩应覆盖显示器的顶部和两侧。
d. 桌面和键盘:
桌面和键盘应为中性色,且反射率应较低。遮光罩的顶部深度应适中,从显示器面板到遮光罩前缘应有足够距离,但不应显得压迫观察者。
颜色差异容差:
通过 ISO 12647-7 控制条测试,测量显示器表征印刷条件和实际测量值之间的色度差异。表征印刷条件与测量的显示器颜色之间的ΔE00应符合表3规定的容差。
4.4 Display driving and simulation requirements(显示驱动和模拟要求)
4.4.1 General(总则)
首先,应按照制造商的要求对显示器进行校准,并可以对软打样系统进行视觉微调。
对于每种需要测试的表征印刷条件,仅显示附录 B 中列出的色块以及任何需要的专色色块。这些色块的最小尺寸应为 10 cm × 10 cm。这些色块应按顺序放置并在预定观察平面中心进行测量,以检查模拟的准确性。如果需要再现专色,则应使用均匀的显示色块,且其测试方法与上述色块一致。
显示的色块应满足比 ISO 12647-7 规定更严格的容差,即模拟表征印刷条件的色块应符合以下要求:
• 平均ΔE00 ≤ 2
• 最大ΔE00 ≤ 3
• 每个专色色块的ΔE00应≤1.5
注: 对于许多软打样系统来说,使用 A4 尺寸的样张便于测量和操作。
4.4.2 Testing of display driving(显示驱动的测试)
4.4.2.1 General(总则)
软打样系统应调整输入的图像内容数据,使显示器的颜色(通过光谱辐射计测量)与内容数据文件所关联的表征数据定义的色度一致。色块应在显示器中心按顺序显示和测量,中心定义为距显示器内边框至少1/4长度的区域,包括显示器最内侧的1/4部分。
为了测试显示驱动,应使用用于校准和配置系统的测量设备(光谱辐射计或色度计,可接触或非接触式)。如果使用特定系统的校准,则应记录校正的测量值(与参考测量设备匹配,以反映正常视力观察者的差异),而不是原始测量数据。
• 注1: 内置色度计的显示器可用于测量显示器的中心外部区域,前提是色度计已通过可靠设备校正与显示器中心的测量一致,并提供重新校正的方法。
• 注2: 系统特定校准指的是对特定类型的显示器和/或测量设备应用的校正(用于补偿系统效应)。这种校正通常用于软打样系统,例如 Kodak 或 Remote Director 系统。
4.4.2.2 Colorimetric accuracy(色度精度)
色度精度通过显示器的 ICC 配置文件或其他颜色变换方法的表征准确性来评估,包括以下两个测试:
1. 显示并测量附录 A 中定义的 318 个 RGB 色块,测量值与配置文件预测值之间的色差(基于绝对色度呈现)应符合表 1 中的容差。
• 参考印刷条件的色域内颜色应显示并测量,ΔE00 应 ≤ 2.5。

表 1 – 基于附录 A 中 RGB 集的配置文件精度容差
标准 RGB 代码值 容差
配置文件精度 全部 平均 ΔE00 ≤ 2.5
99 百分位 ΔE00 ≤ 4.5
2. 显示并测量 ISO 12647-7 中定义的超出色域的色块,容差规定在表 2 中。
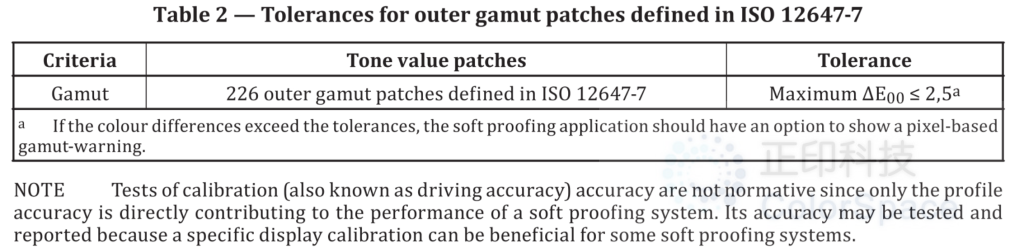
表 2 – ISO 12647-7 中超出色域色块的容差
标准 色调值色块 容差
226 个超出色域色块 最大 ΔE00 ≤ 2.5
• 注: 校准精度的测试(也称为驱动精度测试)不是强制性的,因为只有配置文件精度直接影响软打样系统的性能。然而,对于某些软打样系统,特定的显示器校准可能是有益的。
4.4.2.3 Uniformity evaluation(均匀性评估)
均匀性评估是软打样系统性能的重要部分,包括对显示器屏幕上的纯色和色调渐变进行检查。具体要求如下:
4.4.2.3.1 General(总则)
显示器的均匀性对于软打样系统至关重要。均匀性应针对以下方面进行评估:
• 纯色显示的均匀性(例如白色、灰色);
• 色调渐变的均匀性变化。
在测试均匀性时,应报告显示器的均匀性测试结果。如果显示器具有基于硬件的查找表(LUT)校正功能,则应在测试时开启(如果存在该功能)。
4.4.2.3.2 Evaluation of tone uniformity(色调均匀性评估)
为了评估显示器在不同亮度水平下的色调均匀性,需要在屏幕上定义一个 5×5 的网格(共 25 个区域),并对这些区域进行测量。具体方法如下:
1. 参考白点测量:
• 测量显示器中心区域在最大驱动亮度(R=G=B=255,对8位显示器而言)下的 CIELAB 值,并将其作为参考白点。
• 注意:该方法可能导致某些 CIE L* 值大于 100。
2. 色差计算:
• 比较 5×5 网格中 24 个非中心区域的色差(ΔE00)与中心区域的参考值。
• 测试在以下三个不同驱动亮度级别下进行:
• 白色: 最大驱动亮度(R=G=B=255);
• 中灰: 大约为最大驱动亮度的一半(R=G=B=127);
• 深灰: 大约为最大驱动亮度的四分之一(R=G=B=63)。
3. 色差容差要求:
• 白色和中灰色: ΔE00 色差应 ≤ 4,建议值为 ≤ 2。
4.4.2.3.3 Tonality evaluation (uniformity)(色调均匀性评估)
为了进一步评估色调均匀性,需使用亮度(cd/m²)测量结果进行计算:
1. 测量灰白比:
• 测量 5×5 网格中所有区域的灰色(R=G=B=127)和白色(R=G=B=255)亮度比。
• 计算网格中心区域的灰白比,并将其作为基准值(Rc)。
2. 计算各区域偏差(Ti):
• 对于每个非中心区域 i,其灰白比偏差公式如下:

其中, 为第 i 区域的灰白比, 为中心区域的灰白比。
3. 容差要求:
• 偏差 的最大值应 ≤ 10%,即:
4.4.3 Testing of the simulation(模拟测试)
模拟再现质量的测试旨在评估软打样显示系统再现参考印刷条件的能力。测试步骤和要求如下:
测量设备与环境控制
1. 测量设备:
• 测试应使用遥测光谱辐射计或接触式光谱辐射计进行。
• 如果使用接触式光谱辐射计,应报告环境光对测量的影响,以及与杂散光(光晕)相关的不确定性。
2. 测量条件:
• 使用遥测光谱辐射计时,其接收光锥的孔径应符合 ISO 12646 的规定。
测试过程
1. 显示色块的测量:
• 依次显示附表 B.1 中定义的色块(包含色调值)。
• 使用测量设备逐一测量显示器中心的每个色块。
2. 打印色块的测量:
• 将附表 B.1 中定义的色块按顺序放置在预定观察平面上,并逐一测量其颜色数据。
色彩匹配要求
1. 视觉匹配与色度数据:
• 尽管视觉匹配可能显示一致性,但 CIEXYZ 值可能存在差异。
• 如果存在仪器测量结果的偏差,应对显示器的测量值进行适当的校正。
2. 校正方法:
• 校正应在以下条件下进行:
• 打印的白色色块与模拟白色色块之间的ΔE00 ≤ 5。
• 亮度差异小于 15%(以较大值除以较小值计算百分比差异)。
• 如果任一差异超过上述容差,且系统无法进行调整,则视为不满足本条款要求。
3. 软打样与打印样品的色度精度:
• 软打样显示系统与印刷样品之间的ΔE00色差应符合表 3 中的规定。

表 3 – 参考印刷与软打样再现之间的ΔE00容差
附加要求
1. 专色色块的再现:
• 本国际标准仅限于可均匀分布的专色(即实色色块,而非渐变色或与其他颜色叠印的专色)。
• 专色色块的再现色差应 ≤ ΔE00 2.5(前提是专色位于软打样显示器的色域内)。
2. 参考白点的使用:
• 计算 CIELAB 值时,应将打印样品中的白色色块(CMYK=0,0,0,0)作为三刺激值的归一化参考点,适用于显示器的测量数据和打印参考样品的测量数据。
3. 对比度评估:
• 计算合同打样的纸白色色块与黑色色块(CMYK=0,0,0,100)之间的 CIEY* 对比度比值。
• 软打样对比度与合同打样对比度的比值应介于 0.5 和 2.0 之间。
4.4.4 Visual(视觉评估)
除了对设备驱动和模拟的客观评估外,还应进行基于视觉的评估。此时,应使用适当的测试表单(例如 ISO 12640 中定义的测试图像和渐变图,或研究机构提供的图像)来检查整体外观模拟。
视觉检查应关注以下方面:
• 平滑性(smoothness);
• 白点(white point);
• 均匀性(uniformity);
• 与参考打印品的视觉匹配度(visual match with a reference print)。
注释:
1. 显示器的色调渐变非常重要,可通过视觉方式检查。当新的检测方法被开发出来时,此项将成为具备可测容差的规范标准的一部分。
2. 某些研究机构免费提供测试图像。
附录 B(Annex B)
测试色块
本附录描述了用于模拟测试和评估软打样系统性能的标准测试色块。这些色块的设置旨在提供全面的色彩覆盖和评估精度。
B.1 色块设计
• 测试色块包括一组 72 个色调值,涵盖 CMYK 和 RGB 颜色空间的关键颜色区域。
• 色块应包括以下特征:
1. CMYK 色块:
• 各种比例的青色(C)、洋红(M)、黄色(Y)和黑色(K)组合,涵盖色域的关键部分。
2. RGB 色块:
• 包括 R、G、B 三个通道的纯色和中间色组合,用于评估屏幕和打印在 RGB 空间的再现性能。
3. 灰度块:
• 一组从黑到白的渐变色块,用于评估色调均匀性和对比度表现。
B.2 色块规格
• 每个色块的最小尺寸为 10 cm × 10 cm,以确保足够的区域进行精确测量。
• 色块的排列应符合特定顺序,便于逐一显示、测量和分析。
B.3 测试方法
1. 显示器上的测试:
• 通过显示设备依次显示色块,并在显示器中心进行测量。
• 测试的每个色块需使用光谱辐射计或色度计采集色彩数据。
2. 打印样本的测试:
• 将色块以相同顺序打印并放置在观察平面内。
• 测量每个打印色块的颜色值,以与显示器结果进行对比。
B.4 数据分析
• 测量的显示器色块和打印色块数据应按以下方式进行对比:
1. ΔE00 色差计算: 测试显示结果与目标色块的色差,评估色彩再现精度。
2. 亮度差异分析: 计算白色色块与灰色色块的对比度,验证软打样对比度表现。
B.5 测试色块的重要性
本附录中的色块设计和测试方法确保了软打样系统在不同颜色条件下的精度和一致性。其结果可作为评估系统性能和调校显示设备的重要参考依据。
Table B.1—显示器模拟色块
Patch# | C | M | Y | K | Patch# | C | M | Y | K | |
1 | 100 | 0 | 0 | 0 | 37 | 40 | 0 | 40 | 0 | |
2 | 70 | 0 | 0 | 0 | 38 | 20 | 0 | 20 | 0 | |
3 | 40 | 0 | 0 | 0 | 39 | 10 | 0 | 10 | 0 | |
4 | 20 | 0 | 0 | 0 | 40 | 10 | 6 | 6 | 0 | |
5 | 10 | 0 | 0 | 0 | 41 | 20 | 12 | 12 | 0 | |
6 | 0 | 100 | 0 | 0 | 42 | 40 | 27 | 27 | 0 | |
7 | 0 | 70 | 0 | 0 | 43 | 60 | 45 | 45 | 0 | |
8 | 0 | 40 | 0 | 0 | 44 | 80 | 65 | 65 | 0 | |
9 | 0 | 20 | 0 | 0 | 45 | 100 | 85 | 85 | 0 | |
10 | 0 | 10 | 0 | 0 | 46 | 100 | 0 | 0 | 100 | |
11 | 0 | 0 | 100 | 0 | 47 | 20 | 100 | 70 | 60 | |
12 | 0 | 0 | 70 | 0 | 48 | 70 | 0 | 70 | 80 | |
13 | 0 | 0 | 40 | 0 | 49 | 100 | 100 | 100 | 0 | |
14 | 0 | 0 | 20 | 0 | 50 | 70 | 70 | 70 | 0 | |
15 | 0 | 0 | 10 | 0 | 51 | 40 | 40 | 40 | 0 | |
16 | 0 | 0 | 0 | 10 | 52 | 20 | 20 | 20 | 0 | |
17 | 0 | 0 | 0 | 20 | 53 | 10 | 10 | 10 | 0 | |
18 | 0 | 0 | 0 | 40 | 54 | 20 | 70 | 70 | 0 | |
19 | 0 | 0 | 0 | 60 | 55 | 40 | 70 | 70 | 20 | |
20 | 0 | 0 | 0 | 80 | 56 | 40 | 100 | 100 | 20 | |
21 | 0 | 0 | 0 | 100 | 57 | 40 | 100 | 40 | 20 | |
22 | 0 | 100 | 0 | 100 | 58 | 40 | 40 | 100 | 20 | |
23 | 0 | 70 | 70 | 60 | 59 | 100 | 40 | 100 | 20 | |
24 | 0 | 0 | 70 | 80 | 60 | 100 | 40 | 40 | 20 | |
25 | 100 | 100 | 0 | 0 | 61 | 100 | 100 | 40 | 20 | |
26 | 70 | 70 | 0 | 0 | 62 | 10 | 40 | 40 | 0 | |
27 | 40 | 40 | 0 | 0 | 63 | 0 | 40 | 100 | 0 | |
28 | 20 | 20 | 0 | 0 | 64 | 0 | 100 | 40 | 0 | |
29 | 10 | 10 | 0 | 0 | 65 | 40 | 100 | 0 | 0 | |
30 | 0 | 100 | 100 | 0 | 66 | 40 | 0 | 100 | 0 | |
31 | 0 | 70 | 70 | 0 | 67 | 100 | 0 | 40 | 0 |
Patch# | C | M | Y | K | Patch# | C | M | Y | K | |
32 | 0 | 40 | 40 | 0 | 68 | 100 | 40 | 0 | 0 | |
33 | 0 | 20 | 20 | 0 | 69 | 0 | 0 | 0 | 0 | |
34 | 0 | 10 | 10 | 0 | 70 | 0 | 0 | 100 | 100 | |
35 | 100 | 0 | 100 | 0 | 71 | 0 | 70 | 0 | 60 | |
36 | 70 | 0 | 70 | 0 | 72 | 70 | 0 | 0 | 80 |
Was this helpful?
2 / 0